ENSCO 71 Power System StudyENSCO 71 is a Jack-Up drilling rig which was originally constructed at the Hitachi Zosen shipyard in 1982. The original GE motor controls comprised five 1163 KVA generators and four 1800 ADC SCR units with associated auxiliary transformer feeders and jacking units. The SCRs were assignable to two 1600 HP twin-motor Mud Pumps, a twin motor 2000 HP Drawworks and a 1000 HP Rotary Table. A separate feeder drives a 1110 HP Top Drive. A fifth SCR was added by Hill Graham Controls in 1985 to power a third 1600 HP Mud Pump, which was cabled to the main busbars.
In early 2012, a decision was made to add a fifth 2500 KVA generator and an additional auxiliary transformer, to close-couple these to the main switchboard via a bus tie circuit breaker, and to include a dedicated feeder for the fifth SCR. A sixth SCR was also included in the switchboard extension to provide an alternative drive source for the third Mud Pump, effectively removing this load from the main switchboard. The switchboard extension, including full integration with the existing GE and Hill Graham equipment, was engineered and built by Zeefax.
Proving the Original System
As well as providing an extension to the main 600 V switchboard, Zeefax also designed, built and commissioned an accompanying 480 V switchboard comprising of an incoming circuit breaker and a number of small moulded case distribution circuit breakers.
The design and engineering process involved completing a detailed Power Study to examine the consequences, in terms of fault rating, of adding the new equipment. Various scenarios were considered, and the financial impact was assessed to determine the most cost effective interconnection configuration. As a result of the study the amount of upgrade work required on the existing equipment was minimised.
The Power System Study was completed by gathering data about the existing switchboard arrangement and comparing this to the original, hand written, fault level calculations. The new calculations were performed using software modelling and verified to IEC 61363. The IEC 61363 Short Circuit study represents conditions that may affect typical marine or offshore installations more significantly than land-based systems, including more emphasis on generator and motor decay. This confirmed the original calculations were accurate.
The consequences of adding the new equipment were then considered and the appropriate decisions made and incorporated into the design.
Co-ordination Study
As well as considering the effects of fault currents, Zeefax also completed a complete protective device co-ordination study to confirm and ensure that proper co-ordination was established for all operating scenarios. This included the existing equipment as well as the components in the switchboard extension, and the new 480 V switchboard and transformer.
Finally, the study also included calculating the strength and current-carrying capacity of the busbars under normal and fault conditions to establish the correct busbar sizes and bracing.
The completed Power Study package was submitted to, and approved by ABS (American Bureau of Shipping).
Co-ordination StudyProtection Device Co-ordination
Protective Device Co-ordination is the process of determining the optimum timing of current interruption when abnormal electrical conditions occur within electrical control panels and systems. The goal is to minimize unscheduled or unexpected power outages, by ensuring that if and when a fault occurs, the installed fuses and circuit breakers will operate in a timely manner AND in the right order. This is especially important for Drilling and related applications, and Zeefax can provide a comprehensive Coordination Study service for all type and manufacturers of MCCs.
Until recently, protective device coordination studies would have been laboriously performed manually, using translucent log-log paper, but modern computer methods have enormously streamlined the process, reducing the time and the cost of a comprehensive study, thereby making system coordination studies a realistic proposition for almost any electrical installation.
Using advanced software routines, our expert analysts can produce optimised system response reports, including a selection of graphical and tabular displays , intended to enable the plant owner to fine tune each protection device to meet the specific operational and protection needs of the plant.
Reports include time vs. current coordination drawings, one-line diagrams and a complete schedule of device settings, highlighting individual response time settings for each breaker and for each fuse in the shutdown regime.
Furthermore, if components require updating, the report includes detailed recommendations and specifications for suitable devices, each carefully selected and dynamically re-modelled to ensure accurate and reliable protective co-ordination between electronic and thermal devices when installed.
This dynamic technique may be applied to almost any electrical power system including utility, industrial, commercial, manufacturing, and process systems, and device responses may be plotted at any voltage, current or application frequency.
Key Benefits
The benefits are:
- Design safer power systems by quickly and easily evaluating all devices for proper short circuit levels, and application within acceptable voltage ratings.
- Save time with automatic TCC drawing and associated one-line creation from the main one-line diagram.
- Eliminate errors by keeping all input data, one-line diagrams, TCC’s and study results in a single project database.
- Communicate designs effectively with high quality graphical output and custom formats.
Standards
Using the advanced software analysis routines, we can perform detailed studies according to the recognized international standards for Vessels and Offshore units (IEC61363) and for land based installations (IEC60909).
These standards define the procedures for calculating short-circuit currents and protection systems for three-phase electrical installations for ships and mobile and fixed offshore units.
Al BzoomEngineering Challenges
After several years of inactivity, the Al Bzoom jack-up was programmed for refurbishment and upgrade, and Zeefax was selected to provide the 600V and 480V switchboards and transformers.
The system to be supplied was not simply a replacement, but represented a substantial increase in generated power, and consequently, Zeefax faced a considerable challenge to engineer a footprint that would fit within the existing switch-room structure. Following extensive consultation with the client, a U-shaped format was adopted for the main 600V switchboard.
The main 600V switchboard comprises four 2.5 MVA generator control sections with Woodward and Basler digital controllers; these provide the generator frequency regulation as well as managing the voltage and load sharing. The five SCR sections incorporate DCS800 ABB digital drives and are fully assignable for drilling operations. The SCR sections also incorporate AC line reactors, DC motor isolators, and DC interconnections, so for installation, no additional equipment or cabling is required other than connection to the DC motors.
The whole system was engineered and built at our manufacturing facility in the UK, where we are able to design and construct complete SCR systems based on older style analogue controllers (Hill Graham/Ross Hill type) or on more contemporary fully digital configurations of our own design; the Al Bzoom system is fully digital.
Digital Control
A distributed digital I/O network provides the communications link for all elements of the SCR system, including the Driller’s console, the Mud Pump console, the drilling and auxiliary MCCs, and the central graphical interface, which is used to monitor and control operations. The Driller’s console connection is made using a dual fibre-optic cable, whilst the Mud pump console and MCCs are connected using screened twisted pair cables. The communication protocols are industry standard MODBUS and PROFIBUS, enabling full integration of this SCR system into other SCADA and distributed control networks.
Project Management
As well as engineering and manufacturing the main 600V SCR switchboard, Zeefax was also responsible for providing all of the major electrical distribution components for the rig. The necessary approval was obtained through ABS and all of the required drawings, calculations and co-ordination settings were provided by Zeefax.
The scope of supply included the following main assemblies:.
- 600V Switchboard : Comprising, four 2.5 MVA generator sections; five assignable SCR sections with DC isolators; two 2.5 MVA transformer feeders; three jacking feeders and top drive feeder.
- 480V Switchboard : Comprising two incoming sections and interlocked bus tie, with various feeders for 480V MCCs and distribution boards.
- 480V MCCs : Comprising the main MCCs A and B; the ventilation MCC; the drilling MCC and the Auxiliary MCC.
- Power Transformers : Comprising two 2.5 MVA 600:480V enclosed transformers and 480:220V distribution transformers.
- Control Consoles : Comprising the Driller’s Console (hazardous area); the Foot Throttle (hazardous area); the Mud Pump Console and the PLC control section.
Mindi Dredger, PanamaThe Mindi Dredger
This hard working dredger has been active since 1943 and has recently undergone a major refurbishment program; this included replacement of the control modules which were nearing the end of their lives, and which had been recognised as a critical point of failure.
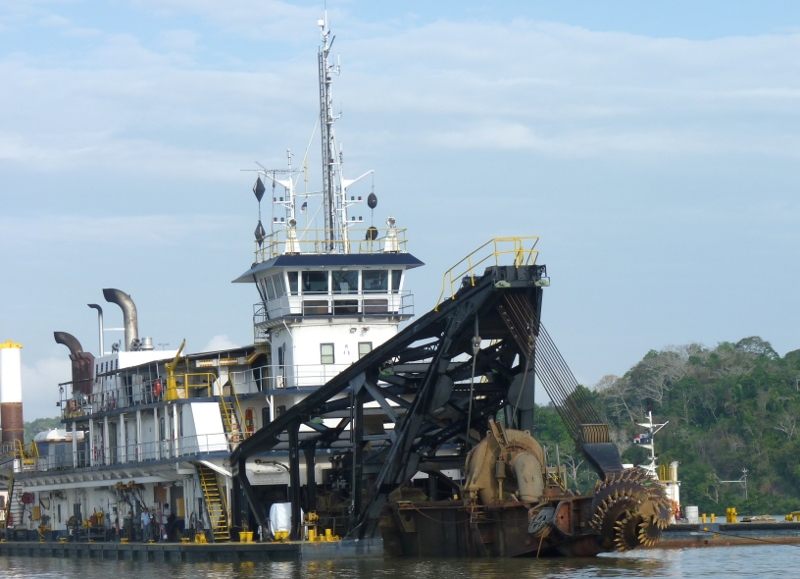
The Mindi Cutter-Suction dredger is more than 400 feet long and is currently powered by three generator sections, providing a total of up to 3.5 MW of electrical power; she also has two large diesel powered pumps.
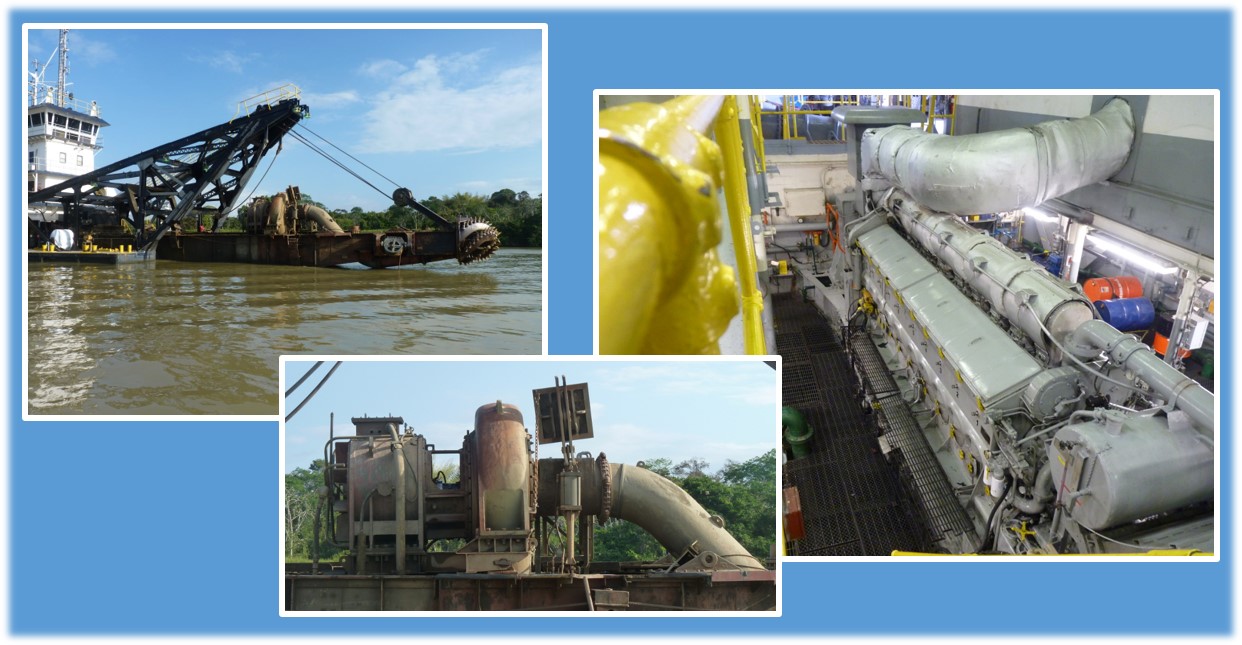
The generators feed a large Direct-on-Line pump for removing the dredged spoil and two Transformer Feed sections, with a Bus-Tie breaker to connect the two separate bus systems together. The plant was controlled using legacy motor control equipment and three first generation AutoSync AC Control Modules, all installed in mid 1980s.
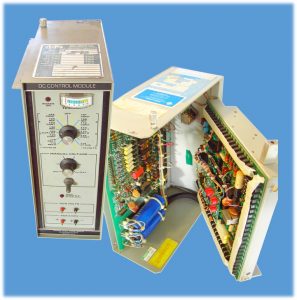
The Panama Canal
The Panama Canal, built thanks to engineering ingenuity, and enormous financial and political persistence, has become one of the greatest benefits to world commerce. Ships passing between the Atlantic and the Pacific oceans can save up to 8000 nautical miles by taking this shortcut; they also avoid the perils of passing round Cape Horn, with its legendary violent seas and hazardous currents. Since opening in August 1924, more than one million vessels have passed through the waterway, each paying a toll to ensure the continued availability of the canal. This vast man-made waterway across the Panamanian isthmus, is almost 51 miles long; it has three sets of massive locks and various lakes, and a fleet of tugs and dredgers which work tirelessly to keep vessels moving and the canal free of debris and landslide spoil. During the early 2000s, a replacement Dredger was acquired with the intention of scrapping the Mindi. However, recent activity to deepen and widen the canal has highlighted the reliability and robustness of the Mindi dredger and a program to extend the useful life of this valued asset was commenced.
New Digital AutoSync Modules from Zeefax
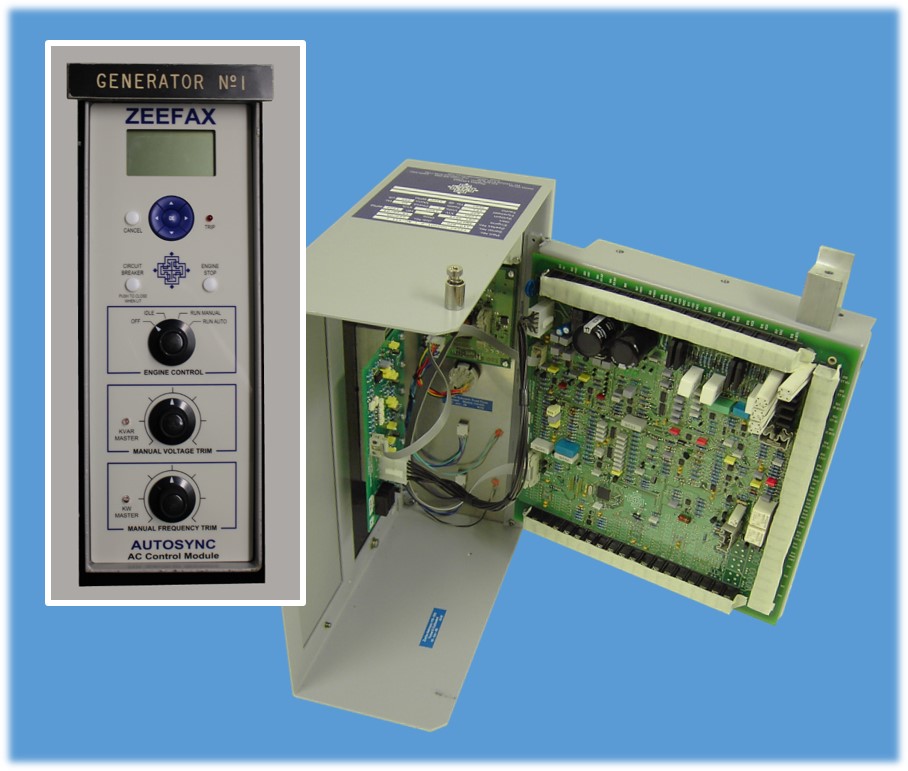
Zeefax was identified as the only viable supplier to replace the aging modules and was awarded a contract for the design, manufacture, installation and commissioning of 3 new Digital AutoSync modules (plus a spare). The contract also included the redesign of the Tie Breaker Control System which was proving increasingly unreliable. The successful installation was performed by Zeefax engineers, who worked with the local engineers to install, commission and operationally test the new equipment.
Zeefax is now the preferred global supplier for all Hill Graham services and manufactured parts, as well as providing a host of other related Drilling services. Please call us to find out more about how we can help to preserve your capital investment, through a program of works, carefully designed to optimise the utility and the performance of your Power System, whilst ensuring that it provides reliable and dependable operation for all your drilling applications.
Maersk Gallant RefurbishmentMaersk Gallant SCR Upgrade
Comprising 11 separate 1600A DC Drive cabinets and a PLC based control panel, the system is equipped to control up to 6 mud pumps, 3 draw-works motors and two top drives when fed from a 6000 A bus.
A key factor in the purchasing decision was the very limited space available for the installation of the new cabinets. Zeefax worked closely with the end user to design and build a system with a very small footprint, and had to overcome a series of technical design challenges to fulfil the brief. The high voltage bus bars were tightly packed into the small cabinets, necessitating careful positioning and design of the forced air cooling system.
Together with a full range of standard SCR control equipment, the system also includes field reversing on Draw-works A and on both Top Drives, and each control panel features a state-of-the-art Digital DC motor controller (DDC). Zeefax designed and built all of these panels in our development and production facility based in Bracknell, England. Prior to shipment, a full series of factory acceptance tests were performed and witnessed by the customer, during which the quality of workmanship was especially praised.
All new Digital DC Control Module
The all new feature packed DDC control module from Zeefax is the next generation module, and includes a comprehensive array of configurable parameters, making it suitable for all types of motors commonly found on board drilling rigs. The unit has been designed specifically with existing system replacement and upgrade in mind, being physically identical to older legacy units. This means that system upgrades are simple, and generally will not need extensive panel remodelling or wiring re-work.
SCR Simulator for NaftogazFull Sized SCR Training Simulator
Zeefax recently designed, built and delivered the world’s first full size SCR Training Simulator for Naftogaz, the National Oil and Gas Company of Ukraine.
This fully functional SCR Simulator provides the most realistic training and assessment experience currently available for rig operators and managers of all skill levels, encompassing all operational and maintenance scenarios. The system enables a comprehensive list of fault conditions to be tested, such as generator load sharing faults and power limit problems, as well as simulation of many diverse operating regimes, including generator start-up, shut down, and synchronisation.
Furthermore, combinations of assignments, allowing simulation of Mud Pumps, Drawworks, Rotary Table, dynamic braking, and auxiliary motor control, may be mimicked, thereby providing exact matching of actual operational conditions.
Key Features
Key features of the system include:-
- Full sized SCR training simulator
- Software Controlled Simulation
- Realistic breakdown scenarios
- Integral performance assessment of trainees
- PLC training and operational simulation station
The 40 foot long, self contained simulator includes operator and instructor work-stations, where trainee activities can be viewed and assessed, and known faults can be selectively introduced during tests and assessments. The Power Control Room also contains a PLC training station, complete with graphical display, facilitating training in the use of PLC controlled systems, including troubleshooting and component replacement.
Big Orange XVIIIBackground to the Project
The Big Orange XVIII support vessel, based in Montrose, Scotland, provides processing and installation support intended to keep oil flowing from the numerous North Sea wells. On board, electric motors are used for both propulsion and well pumping duty; the electrical power for these and the vessel as a whole is provided by three 3200kW diesel generators, and the whole system is managed and controlled by legacy Hill Graham AC and DC modules. Since acquiring HGC, Zeefax has taken over the support and maintenance of this equipment.
SCR Systems
The propulsion system uses two rotatable thrusters to ensure very accurate positioning of the vessel; there is a full complement of compressors and pumps which are used in the well stimulation process, and a total of fifteen 1200kW DC motor drives (SCRs) which control the power to the propulsion units and the pumping motors.
A major feature of the power system is built in redundancy; all three generators are only needed if all drives are at full power, and under normal operating conditions, only two of the generators are required. This means that if needed, the modules and the electronic circuit boards which form the control system can be replaced at sea and sent away for repair when convenient. The ability to turn an engine off when not at full load can lead to significant fuel savings for a ship on this type of duty.
The 15 drives and associated electronic cards and modules which give the vessel the very high degree of control needed, plus the three engine and generator controllers, were all originally supplied by Hill Graham Controls.
All this vintage, but complex, equipment needs highly specialised servicing and engineering support, that Zeefax provides from our design and manufacturing facility in Bracknell, near London.